Paper:
Development of Remote Construction System of Modularized Rail Structure for Inexperienced Operators
Hikaru Terashima, Koki Honda
, Ryota Yokomura
, and Rui Fukui

Department of Human and Engineered Environmental Studies, Graduate School of Frontier Sciences, The University of Tokyo
5-1-5 Kashiwanoha, Kashiwa-shi, Chiba 277-8563, Japan
Remotely controlled robots are required to operate in human-inaccessible environments, such as the decommissioning of nuclear power plants. In our previous studies, we proposed a modularized rail structure for such environments. In long-term decommissioning work at a nuclear power plant, robots are controlled by inexperienced operators who have limited knowledge of the design details of the robots. In this study, we developed a remote construction system for supporting inexperienced operators by transmitting the status information of the constructor robot to the operator during the remote construction of a modularized rail structure. The proposed remote construction system was designed based on a human information-processing model. Experiments were conducted using the developed remote construction system. The proposed method achieved a success count of inexperienced operators equivalent to that of skilled operators. Furthermore, a questionnaire administered to participants showed that their cognitive, psychological, and physical loads during construction were sufficiently low during the experiment.
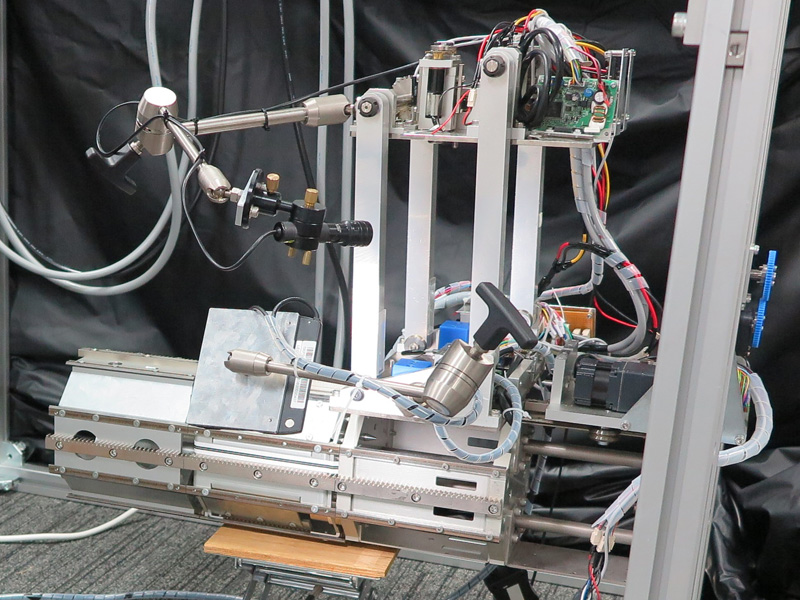
Remote construction of modularized rail structure
- [1] K. Chayama, A. Fujioka, K. Kawashima, H. Yamamoto, Y. Nitta, C. Ueki, A. Yamashita, and H. Asama, “Technology of Unmanned Construction System in Japan,” J. Robot. Mechatron., Vol.26, No.4, pp. 403-417, 2014. https://doi.org/10.20965/jrm.2014.p0403
- [2] T. Ikeda, N. Bando, and H. Yamada, “Semi-Automatic Visual Support System with Drone for Teleoperated Construction Robot,” J. Robot. Mechatron., Vol.33, No.2, pp. 313-321, 2021. https://doi.org/10.20965/jrm.2021.p0313
- [3] A. A. Yusof, M. N. A. Saadun, H. Sulaiman, and S. A. Sabaruddin, “Modern practical application and research on teleoperated excavators control, feedback and perception issues in post disaster recovery operation,” Proc. of the 2015 IEEE Int. Symp. on Robotics and Intelligent Sensors (IRIS), pp. 179-185, 2015. https://doi.org/10.1109/IRIS.2015.7451608
- [4] F.-C. Chen and M. R. Jahanshahi, “NB-FCN: Real-Time Accurate Crack Detection in Inspection Videos Using Deep Fully Convolutional Network and Parametric Data Fusion,” IEEE Trans. on Instrumentation and Measurement, Vol.69, No.8, pp. 5325-5334, 2020. https://doi.org/10.1109/TIM.2019.2959292
- [5] Y. Noguchi, M. Saito, T. Maruyama, and N. Takeda, “Design progress of ITER blanket remote handling system towards manufacturing,” Fusion Engineering and Design, Vol.136, Part A, pp. 722-728, 2018. https://doi.org/10.1016/j.fusengdes.2018.03.068
- [6] H. Roozbahani and H. Handroos, “A novel haptic interface and universal control strategy for Int. thermonuclear experimental reactor (ITER) welding/machining assembly robot,” Robotics and Computer-Integrated Manufacturing, Vol.57, pp. 255-270, 2019. https://doi.org/10.1016/j.rcim.2018.12.011
- [7] R. Gilhooly, “Deep Inside Fukushima,” New Scientist, Vol.226, No.3017, 2015. https://doi.org/10.1016/S0262-4079(15)30164-0
- [8] T. Yoshida, K. Nagatani, S. Tadokoro, T. Nishimura, and E. Koyanagi, “Improvements to the Rescue Robot Quince Toward Future Indoor Surveillance Missions in the Fukushima Daiichi Nuclear Power Plant,” K. Yoshida and S. Tadokoro (Eds.), “Field and Service Robotics,” pp. 19-32, Springer Berlin Heidelberg, Berlin, Heidelberg, 2014. https://doi.org/10.1007/978-3-642-40686-7_2
- [9] L. Morikawa, T. Hashimoto, N. Shimonabe, M. Yano, H. Onitsuka, and J. Fujita, “Development of the remote decontamination robot “MHI-MEISTeR II” for an upper floor of reactor building in Fukushima Daiichi NPP,” E-J. of Advanced Maintenance, Vol.9, No.2, pp. 126-131, 2017.
- [10] H. Yatsuzuka, “The Human Interface of Dual-Arm Heavy Machinery Type Robot “ASTACO-SoRa” for Nuclear Power Plants,” J. of the Robotics Society of Japan, Vol.33, No.6, pp. 404-407, 2015. https://doi.org/10.7210/jrsj.33.404
- [11] R. Fukui, Y. Kato, R. Takahashi, W. Wan, and M. Nakao, “Automated Construction System of Robot Locomotion and Operation Platform for Hazardous Environments—Basic System Design and Feasibility Study of Module Transferring and Connecting Motions,” J. of Field Robotics, Vol.33, No.6, pp. 751-764, 2016. https://doi.org/10.1002/rob.21561
- [12] R. Fukui, K. Kawae, Y. Kato, and M. Nakao, “Rail Structure Supporting Mechanism Using Foamable Resin for Pillar Expansion, Anchoring, and Fixation,” J. Robot. Mechatron., Vol.28, No.2, pp. 129-137, 2016. http://doi.org/10.20965/jrm.2016.p0129
- [13] T. Takano, A. Ikeda, I. Abe, and T. Kikuchi, “Improvement of Haptic Interface for Teleoperation Endoscopic Surgery Simulators Using Magnetorheological Fluid Devices,” J. Robot. Mechatron., Vol.34, No.6, pp. 1268-1276, 2022. https://doi.org/10.20965/jrm.2022.p1268
- [14] R. Yokomura, S. Warisawa, and R. Fukui, “3-Dimensional construction of the modularized rail structure in various posture conditions,” Advanced Robotics, Vol.36, No.24, pp. 1351-1364, 2022. https://doi.org/10.1080/01691864.2022.2132832
- [15] R. Yokomura, H. Terashima, M. Ishiguro, S. Warisawa, and R. Fukui, “Remote construction support for Modularized Rail Structures by visualization of relative position posture and contact state,” Proc. of 40th Annual Conf. of the Robotics Society of Japan, 4A1-04, 2022 (in Japanese).
- [16] Research Institute of Human Engineering for Quality Life, “Usability of Interactive Systems,” MARUZEN Inc., 2005 (in Japanese).
This article is published under a Creative Commons Attribution-NoDerivatives 4.0 Internationa License.