Introduction
Fillet welds are the most commonly used weld types in marine structures. A fillet weld is used when there are two pieces of metal that are joined perpendicular to each other or at an angle. In this article, we will explore how to select the right size fillet weld for the case when the pieces of metals are to be welded perpendicular to each other in a tee-joint. The article follows the requirements of Eurocode 3: Design of steel structure (EN 1993 Part 1)
Weld Geometry
The fillet weld explored in this article is one that is between an incoming member and an endplate. This is shown in the figure below. The incoming member can have a different section shape: it can be an I-section or an RHS section (Rectangular Hollow Steel) or some other section. The method described in this article is only applicable to double symmetrical sections.
Material Properties
The material properties that are relevant will be the properties of the plate, and of the weld.
For the plate, the Yield Strength, Tensile Strength, and the material factor. The material factor γ is a safety factor that is applied based on EN 1993-1-1
For the weld, the Ultimate Strength is used for strength checks, together with a material factor γ and a correlation factor β that are applied based on EN 1993-1-1 and Table 4.1 of EN 1993-1-8 respectively.
Forces
Next, we take a look at the forces on the weld. Any structure will be subject to 6 degrees of freedom, each designated by a force/moment. The weld is subject to the following:
- Axial force
- Shear force, Y-direction
- Shear force, Z-direction
- Moment about X-axis
- Moment about Y-axis
- Moment about Z-axis
Weld Properties
The section properties of the weld need to be computed for the stress checks to be done. These include the bearing area, shear areas, the moment of inertia about the two axes, and the section moduli about the two axes. Depending on whether the section is an RHS section or an I-section, the formulae for these properties will vary.
Stress Checks
Once the section properties are calculated and the forces on the weld are available, we need to perform the stress checks on the weld.
There are different types of stresses that need to be checked:
- Stress due to Axial Force – the axial force (Fx) leads to two types of stresses – one is the normal stress which is calculated by dividing the axial force by the axial cross-sectional area of the weld. The other stress due to the axial force is the shear stress which is also the same as the
- Stress due to Shear Force – the forces in the other two directions, if Fy and Fz lead to shear forces on the weld. The shear force is calculated by dividing the shear force by its respective shear area, i.e.,
Shear Stress due to Fy = Fy/(Shear area in the y-direction)
Shear Stress due to Fz = Fz/(Shear area in the z-direction)
- Stress due to Moments – the three moments along the three axes each produce a different type of stress on the weld, and these can be summarized as below:
- The moment about the Y-axis produces normal stress as well as shear stress that can be calculated by dividing the Moment by the relevant section modulus about the Y-axis
- The moment about the Z-axis produces a normal as well as shear stress that can be calculated by dividing the Moment by the relevant section modulus about the Z-axis
- The moment about the X-axis (axial moment) produces torsional shear stress that can be calculated from the formula
Torsional Shear Stress = Axial moment x extreme axial distance/polar moment of inertia
The axial distance and the polar moment of inertia depend on the type of section selected, and can be calculated using standard formulae for the I-section or RHS section
Final Stresses on the Throat Section
The final stresses on the throat section of the weld can be summarized as below:
- Normal stress perpendicular to the throat σ⊥ – this is a sum of the individual normal stresses due to the axial force Fx, and normal stresses arising from the moments My and Mz
- Shear stress perpendicular to the axis of the weld τ⊥ – this is the sum of the shear stress due to the axial force Fx, and the shear stresses due to My and Mz
- Shear Stress Parallel to the axis of the weld τǁ – this is the sum of the shear stress due to Fy, shear stress due to Fz and the torsional shear stress due to Mx
Acceptance Criteria
The criteria check against allowable stresses are provided below. These need to be met for the weld to be acceptable
- Combined Stress check: the combined stress [σ⊥2+3(τ⊥2+τǁ2)]5 must be less than the allowable combined stress. Allowable combined stress = Ultimate Weld Strength/(Material Factor for weld x correlation factor for weld)
- Normal Stress Check: the normal stress should be less than the allowable normal stress. Allowable normal stress = 0.9 x Ultimate Weld Strength/Material Factor for weld
References
- Eurocode 3: Design of steel structure; Part 1-8: Design of joints
- Eurocode 3: Design of steel structure; Part 1-1: General rules and rules for buildings
- https://en.wikipedia.org/wiki/Fillet_weld
That brings us to the end of this article. Please do check out TheNavalArch’s product on weld design for fillet welds.
Disclaimer: This post is not meant to be authoritative writing on the topic presented. thenavalarch bears no responsibility for the accuracy of this article, or for any incidents/losses arising due to the use of the information in this article in any operation. It is recommended to seek professional advice before executing any activity which draws on information mentioned in this post. All the figures, drawings, and pictures are property of thenavalarch except where indicated, and may not be copied or distributed without permission.
https://thenavalarch.com/software/maritime-industry-thenavalarch/ship-design/ship-strength/weld-check-spreadsheet-joint-sections/

TRANSPORT VESSELS FOR FLOATING WIND
By Alan Crowle, BSc, MSc, CEng, CMarEng, FRINA, FMAREST, FSCMS Masters by Researcher, University of Exeter, College of Engineering, Mathematics and Physical Sciences, Renewable Energy Group SUMMARY Floating wind turbine construction is a large logistical exercise. The...

Using simple tools for efficient Passage Planning for seagoing vessels
Introduction Planning a vessel’s voyage is a critical detailed exercise, and the main goal is to ensure safe and efficient passage between two ports. The Master has the responsibility for the vessel voyage planning, but very often he delegates the actual voyage...
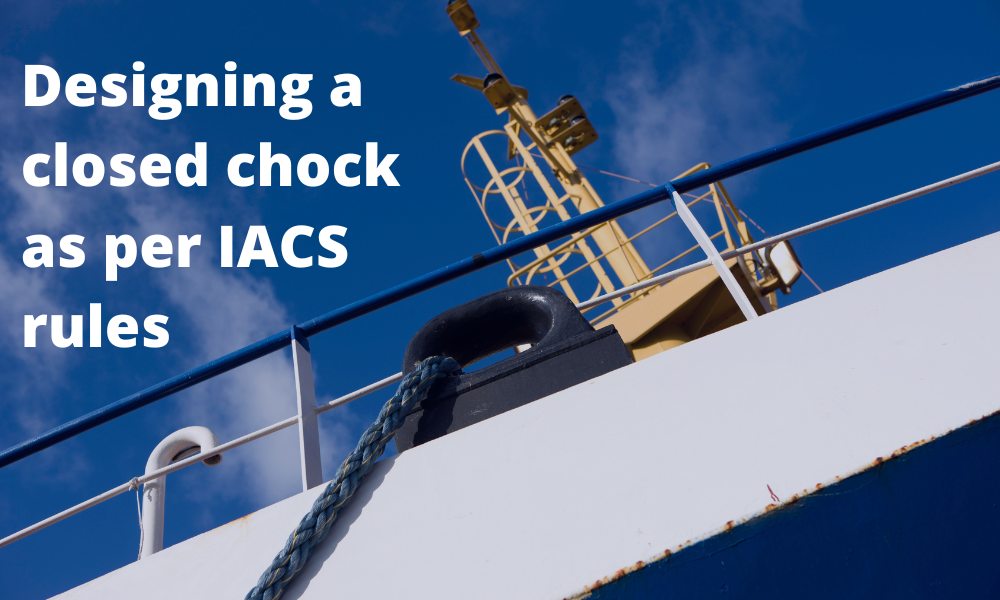
Designing a closed chock as per IACS rules
Introduction Chocks are used universally for mooring and towing operations on ships. For towing operations, Chocks are used for guiding the towing rope from the winch through the outer shell of the vessel to the tug. For mooring operations, the chock is used to...

The Optim22 Method of Weight Optimization of Framed Steel Structures
1 Abstract A semi-automated structural weight optimization system is presented for framed structures of post and beam construction which is based on basic structural member design principles. The approach is to adjust member properties in a manner that...

How to identify the spoolpiece lifting points?
In the offshore construction industry, the connection between the newly installed pipeline and the riser is accomplished via a series of ‘spoolpieces’ (or spools). The spool is fabricated by welding pipe joints to form an L-shaped, Z-shaped, or possibly a straight...

Sea Pressure Loads Calculation based on DNV Rules
Introduction Sea pressure loads are an important factor in the structural design of a vessel. What is sea pressure load? As the term suggests, it is the external pressure on the vessel due to the surrounding sea. What kind of pressure it is, and how to...

Designing a stanchion/stopper for sea-fastening of deck cargo
Introduction Stanchions – a familiar term for mariners and ship designers. What are Stanchions? A stanchion is generally a vertical pipe or beam which is used to support some structural item or provide support rails on the deck. In ships, the most common type of...
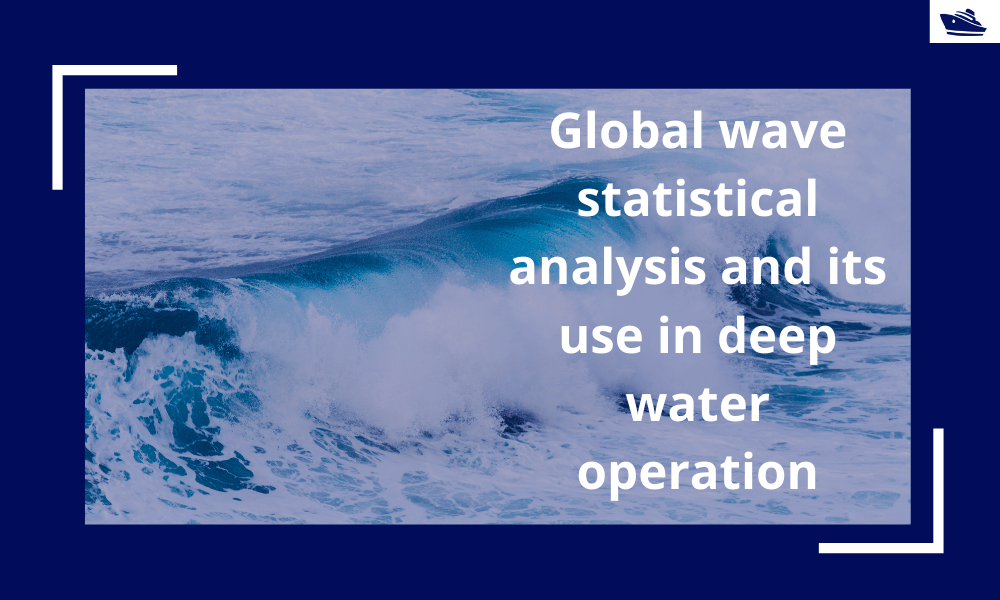
Global wave statistical analysis and its use in deepwater operations
Why do we need wave analysis? For the design of offshore operations such as installation and transport of offshore structures, as well as lifecycle design of floating and fixed structures, knowledge of extreme waves as well as the probability of different sea-states...

Designing a clip/dog plate for seafastening
Introduction In an earlier article, we saw how to design stoppers for seafastening. Stoppers are items that are used to contain the translation movements (longitudinal and transverse directions) of a cargo on the deck/hold of a vessel. That brings us to the question –...
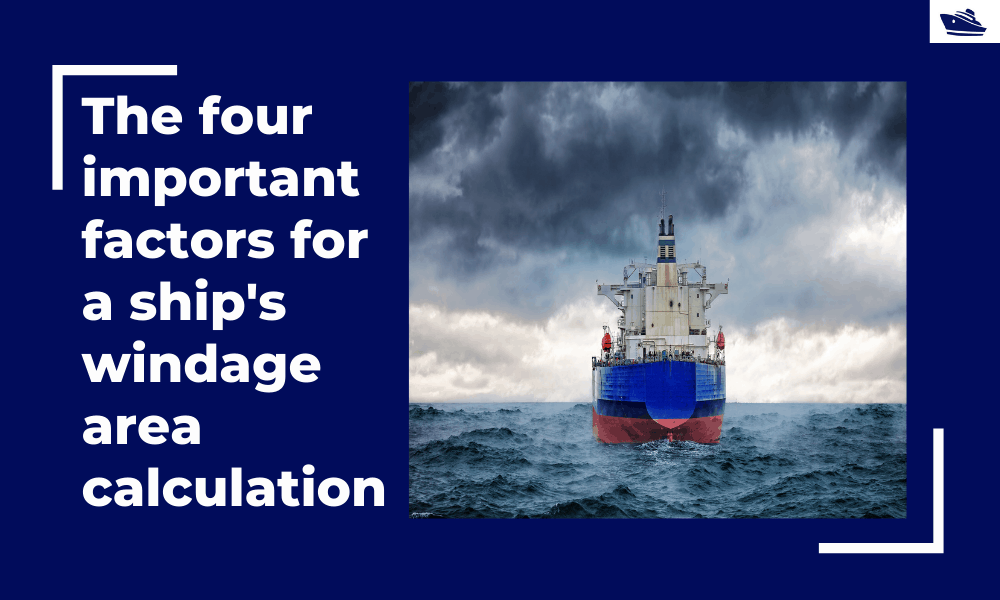
The four important factors for a ship’s windage area calculations
Introduction The windage area of a vessel or offshore structure is the area that is exposed directly to the wind. As is obvious, this is the area of all items above the waterline. This will include Part of the hull/offshore structure above the waterline...
Hey