A paper recently published in the journal Polymers demonstrated the feasibility of using a modified polyethylene (PE) foam to fabricate seamless insulation shells in critical environmental conditions, specifically polar regions.

Study: Modified Polyethylene Foam for Critical Environments. Image Credit: Ilya_Kuznetsov/Shutterstock.com
Background
Foamed polymers are typically used as thermal insulation in structures present in extremely humid environments or direct contact with the ground as they demonstrate low water and vapor permeability and thermal conductivity in different humid conditions and over a significant duration.
Expanded polyurethane and polystyrene foam-based products are used extensively in construction. Polyolefins, including PE foams and polyisocyanurate foams, are also witnessing a rise in adoption in thermal insulation applications.
However, the high flammability is a significant disadvantage of these materials, which necessitates the development of technologies to reduce their flammability and increase their resistance to changing and negative temperatures.

Insulation of sports facilities: (a) ice rink; (b) ice stadium. Image Credit: Ter-Zakaryan, K. A et al., Polymers
The development of special construction systems and technologies is one of the top priorities for every territory located in permafrost areas and country located beyond the Arctic circle, such as Greenland, the United States of America (USA), and Russia.
Insulation systems, such as PE foam-based seamless insulation shells, fully meet the requirements of polar regions. However, addressing the structural issues caused by the use of foamed polymers in buildings and ensuring proper disposal of waste PE foams generated after use is necessary before using them for thermal insulation on a large scale.
Foamed PE is an elastic and soft gas-filled thermoplastic polymer with shock-absorbing properties, high operational stability, and enhanced moisture resistance. The foam is typically used in building structures as a vibration-damping material or lining in five mm-thick sheets or rolls. The foam is also used to prepare seamless insulation shells with high insulating capacity.
Seamless trays based on rolled PE foams have already demonstrated their effectiveness in cold storage applications. The thermal and chemical resistance of foamed PE can be improved using fluorination, bromination, and chlorination. Benzophenone and carbon black derivatives can also be added to PE foams to reduce aging due to ultraviolet radiation and sunlight.
Additionally, the flammability of foamed polymers can be reduced using physicochemical or chemical methods. For instance, foaming gases, such as isobutane, can be replaced with non-flammable gases to reduce the flammability of PE foams.
Although the introduction of ultradispersed mineral powders containing interpacket or intracrystalline water can reduce combustibility, such powders can adversely impact material properties.
The use of recycled PE for PE foam production has gained considerable attention as it is an eco-friendly and sustainable approach. The secondary PE processing includes the collection and storage of waste PE foams, followed by grinding and agglomeration, elimination of foreign inclusions, the addition of modifiers such as flame retardants, and granulation.
Waste generated during PE foam production, such as low-quality products and offcuts, is granulated after being processed through pyrolysis, followed by the addition of modifiers. The PE granulate is then melted in an extruder and mixed with a foaming agent, such as isobutane, continuously under pressure to obtain a polymer mass with a homogenous structure at the molecular level.
Subsequently, a metalized lavsan or a heat-reflecting foil layer is coated on both sides or one side of the finished PE foam rolls. PE foam layers are welded together to realize the monolithic layered products.
Insulating multilayer materials are also prepared in a similar manner, with air gaps between foamed PE layers. These multilayer materials demonstrate lower thermal conductivity compared to monolithic layered materials.
The Study
In this study, researchers developed a method to select an optimized modified PE foam composition, evaluated the flammability and strength of fabricated PE foams and the stability of their properties at low temperatures, and developed insulation systems for building structures in polar regions and locations having permafrost soils.
Specifically, the strength, moisture exposure patterns, thermal conductivity, and operational stability of PE foams with optimized composition were analyzed. The intervals of change in the modifier and flame retardant consumption and recycled PE composition were determined based on a preliminary set of experiments and analysis of prior information.
Researchers determined the factors influencing the reaction functions and their change intervals in the experiment by analyzing scientific sources. These factors included recycled PE consumption, modifier consumption, and flame retardant consumption.
Boron nitrogen compounds and maleic anhydride were used as modifiers, while magnesium oxide hydrate was used as a flame retardant. Both modifier and flame retardant were mixed with recycled PE blend during heat treatment and granulation.
The optimal modified PE foam composition was determined using complete D-optimal schedule-based mathematical design methods using three factors, followed by statistical hypotheses testing and analytical optimization of obtained results.
The average density and the compressive strength of 100 × 100 × 100 mm3 PE foams at 10% deformation were used as response/reaction functions. The compressive strength properties determined the PE foam's operational stability, while the PE foam's average density correlated with the thermal conductivity coefficient.
The compressive strength was also used as an optimization parameter. Flammability tests of the PE foams with an optimized composition were performed based on the “Method for testing combustible building materials to determine their flammability groups” standards.
Eventually, the developed insulation systems were evaluated through graphical visualization. The design solution visualization for insulation systems was performed using a special computer program, two-dimensional building heat-transfer modeling (THERM).
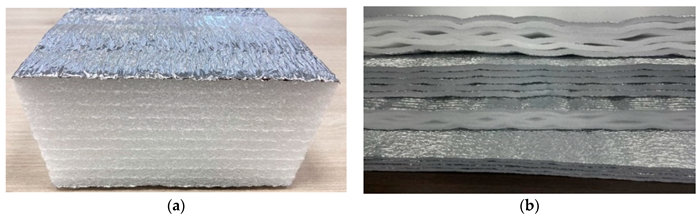
Polyethylene foam products: (a) layered products; (b) multi-layered products with an air gap from the air layer line. Image Credit: Ter-Zakaryan, K. A et al., Polymers
Observations
The average PE foam density primarily depended on the modifier consumption. For instance, the PE foam density decreased with the increasing consumption of maleic anhydride.
However, the average PE foam density slightly increased with the increasing flame-retardant consumption due to the reduction in the melt-foaming effect in the presence of finely dispersed mineral components.
The compressive strength of the PE sheets was positively influenced by the recycled PE consumption, while the modifier flow rate also increased the strength to a small extent. Flame retardant displayed the least positive influence on compressive strength.
Thus, an increase in the value of any factor increased the compressive strength of the PE foam. However, the compressive strength first increased and then decreased with the rising consumption of flame retardant.
The optimal modifier consumption at which the strength was maximum was determined using an analytical optimization method. Although the combined effect of modifier and recycled PE consumption on average density was small, more research must be performed to identify potential antagonistic or synergistic effects of both factors.
A nomogram was constructed using the optimized functions and optimization data to predict PE foam properties, including average density and compressive strength at 10% deformation, based on recycled PE consumption and extruder pressure, and select the recycled PE consumption based on the predicted properties.
500 × 500 × 50 mm3 and 100 × 100 × 100 mm3 PE foam samples with analytically determined optimized plasticizer content of 6.8% of the polymer weight, 11.7 kg/m3 flame retardant, and recycled PE content of 23% of the polymer weight were used to determine the strength and performance properties.
The compressive strength at 10% deformation of the samples was 140–160 kPa at 22–24 kg/m3 average density with 80–92 kPa tensile strength in the longitudinal direction, 29–32 kPa weld strength, 0.032–0.034 W/(m ·K) thermal conductivity, and 0.44 kg/m2 and 0.37 kg/m2 diffusion moisture absorption without and with metalized coating, respectively.
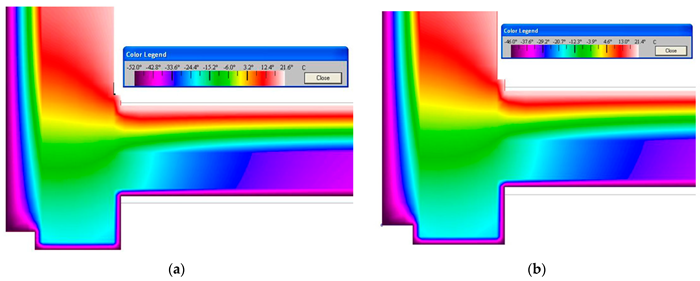
The structure of the formation of the temperature field in a structure isolated above the ventilated space (between the supporting columns): (a)—visualisation of the temperature field for Yakutsk (−52 °C); (b)—visualisation of the temperature field for Norilsk (−46 °C). Image Credit: Ter-Zakaryan, K. A et al., Polymers
The water absorption of the samples was 0.013 kg/m2 when immersed partially for 24 h and 0.96% water absorption by volume when fully immersed in water for 28 days. Moreover, the properties of the foam remained stable under fluctuating temperatures from −60 to 70 oC in the long term.
The PE foam samples with optimized composition displayed 220-230 oC flue gas temperature, with a 15-20 min self-smoldering duration. Additionally, the sample damage length was 10-14%, with a 10-15% weight loss. The foam was moderately combustible, which must be considered while using this foam in building insulation systems.
Overall, the synthesized PE foam performance fully met the requirements for systems and materials used in contact with wet or frozen soil and extremely adverse climatic conditions in polar regions.
To summarize, the findings of this study demonstrated that the PE foam with optimized composition fabricated in this study can be used effectively in insulation systems for pilaf in contact with the ground or seamless insulation shells under a concrete screed for an apartment roof.
Disclaimer: The views expressed here are those of the author expressed in their private capacity and do not necessarily represent the views of AZoM.com Limited T/A AZoNetwork the owner and operator of this website. This disclaimer forms part of the Terms and conditions of use of this website.
Source:
Ter-Zakaryan, K. A., Zhukov, A. D., Bessonov, I. V. et al. Modified Polyethylene Foam for Critical Environments. Polymers 2022. https://www.mdpi.com/2073-4360/14/21/4688