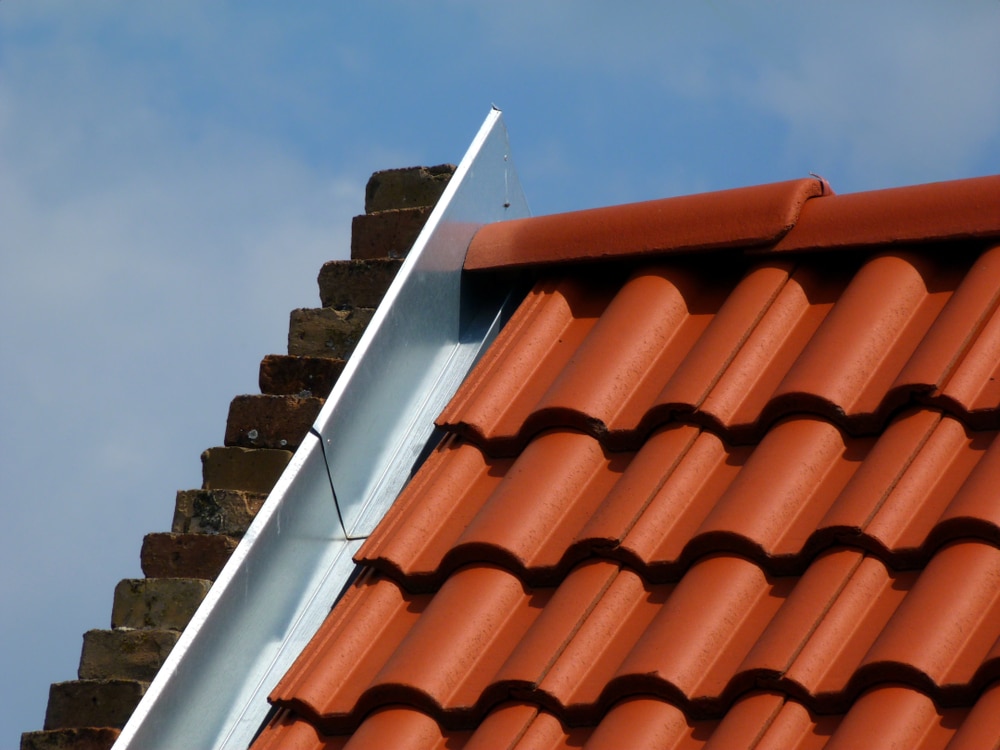
Most of us don’t give much thought to our home’s roof, so roofing terminology usually isn’t in our vocabularies. But one of the most important functions of a home is to provide us with shelter from the elements, including keeping water out, which your roof does tremendously well.
A fully-waterproofed roof helps to avoid serious problems such as rot, mould, and structural damage. Flashing is one of the materials and design elements built into a home’s roof structure to achieve waterproofing, and keep this destructive moisture out. In this article, we’ll delve into the concept of roof flashing, why it’s important, what it’s made of, and more.
What is roof flashing?
Where a roof meets a vertical structure, there are natural weaknesses, including areas of discontinuity like joins and penetrable sections. Penetrable sections include holes or openings in a roof’s surface that allow for structural elements like flues, skylights, vents, and chimneys. Areas where joins occur include gutters, walls adjoining roofs, and door and window frames.
If not properly sealed, these all become entry points for moisture. However, it can be challenging to create an entirely waterproof join between two metal products, or a metal product and a timber product. It can also be difficult to seal areas of penetration as the intersections contract and expand when humidity and temperature changes.
So rather than relying on sealants alone, roofing professionals use flashing as part of a home’s overall weather-resistant barrier system. Flashing is both a device and method for keeping water from entering a structure, and keeping everything sealed while allowing for movement. It forms the terminations and intersections of surfaces and roofing systems, and typically comes as thin pieces of impervious material installed at strategic points on a roof to create a more weather-resistant envelope.
What are the different types of flashing?
Flashing is named according to its shape and how it’s used. There are also different roof flashing types used across the world that are designed to suit certain roof styles and architecture. They include:
- Roof flashing—Placed around objects or discontinuities which protrude from the roof of a building to deflect water away from joints or seams in valleys where water run-off is concentrated.
- Wall flashing—Typically found near windows and points of structural support, it may be embedded in a wall to prevent water entry into a wall or direct water that has penetrated the wall back outside.
- Cap flashing—A concealed flashing used above doors and windows to prevent water from entering walls.
- Sill flashing—A concealed flashing placed under doors or windows to prevent water from entering walls.
- Through-wall flashing—Spans the thickness of a wall and directs water to “weep” (small drainage) holes.
- Kickout flashing—Found at the bottom of a wall or roof intersection and used to deflect water away from the wall.
- Roof penetration flashing—Used to waterproof pipes, cables, supports, cables, and other roof protrusions.
- Channel flashing—Shaped like a “U” to catch water where the edge of a roof meets a wall.
- Apron flashing—Either diverts water from a vertical surface into a gutter or covers the joint between a vertical surface and a sloping roof (at the lower edge of a chimney, for example).
- Valley flashing—Protects the middle section where two roof sections meet, directing rain water run-off away from the roof.
- Roll-top ridge flashing—Covers the ridge (or the high point) where two tiled or metal roof surfaces meet.
- Flat ridge flashing—Similar to roll-top ridge flashing but with a flatter ridge.
- Barge capping flashing—Similar to roll-top and flat ridge flashing, but box-shaped.
- Box guttering flashing—A square or rectangular gutter used within the boundaries of the roof.
- Fascia flashing—Flashing connected to fascias, which adds a decorative finish to a roof’s edge.
- Parapet flashing—A roof and wall flashing covering used to waterproof and cap the ends of masonry walls or vertical sheets.
- Pipe flashing—A thin piece of impervious flashing designed to fit the cylindrical contour of tubes and pipes.
- Step flashing—Pieces of flashing material that overlap each other in “steps”.
Why do buildings need flashing?
There are three ways flashing keeps water out of a roof structure—gravity, wind pressure, and surface tension. It can be installed like shingles (one piece overlapping another) or sealed to function as one continuous surface. Either way, it is designed to prevent water entering a home using surface tension.
Depending on its application, flashing diverts water, penetrating damp, and debris build-up away from potential infiltration points. It is also used on surfaces that are susceptible to leakage, to provide weather-resistance to wall cladding, and on gutters to prevent them over-filling, which can cause damage and encourage the growth of toxic moulds.
What is flashing made of?
Flashing materials can vary considerably and suit a wide range of cost considerations, architectural designs, and compatibility with adjoining materials. In addition to providing a waterproof barrier, flashing should integrate with a building’s design elements. It should also be flexible enough to work into the crevices and contours of a structure where flashings are needed.
Most flashing today is constructed of metal or rubber. Metal flashings materials include aluminium, copper, zinc alloy, stainless steel and lead roof flashing, or coated metals like lead-coated copper, galvanised steel, and anodised aluminium. Flexible flashing materials include acrylic, rubber, rubberised asphalt, and butyl rubber. Flashing is available as roll roofing or in one piece as a membrane, which simplifies installation around roof projections.
In Australia, flashing is typically available in two types: exposed or concealed. Exposed flashing is usually constructed of sheet metal, and concealed flashing of metal or a flexible material if used around wall penetrations like door openings and windows. The most common type of exposed flashing is Colorbond® roof flashing which is pre-painted steel, or unpainted Zincalume® aluminium/zinc alloy-coated steel. Lead replacements such as Wakaflex, rubber or rubberised asphalt is typically used for concealed flashing.
What are the essential elements of flashing?
Flashings are an important part of the design or renovation of any property, from both a practical and aesthetic perspective. Qualified roofing professionals are a critical part of the process when flashing needs to be designed, cut, and fastened. They have the knowledge and expertise to know what flashings will suit certain climate and environmental conditions, and can install it efficiently, effectively, and safely.
Roofing professionals also conform to the Building Code of Australia’s standards, namely, the flashing guidelines contained in the Installation Code for Metal Roof and Wall Cladding (HB39-1997). Important things these guidelines cover include:
Customisation
Although similar metal roof flashing methods are used for different cladding-profiles, flashings (other than standard ridging) are usually designed and manufactured from coil or flat sheet and adapted to suit individual applications. If flashings are required to match the colour of the cladding sheets, pre-painted coils or flat sheets should be made by the same manufacturer using the same process to avoid fading and to ensure sufficient colour matching.
Material compatibility
Flashings and other accessories should be manufactured from the same material used to clad a property’s roof or walls. Run-off from, and contact with, incompatible materials—like treated timbers, chemicals and cleaning agents—can damage coated steel products and cause accelerated corrosion. When incompatible metals are combined, it can also cause a chemical reaction called galvanic corrosion. This can occur when lead and copper come into contact with zinc, aluminium, or coated steel; zinc and aluminium flashing with pressure-treated timbers; and aluminium with wet plaster or mortar.
Wind force resistance
Wind creates considerable force on both the underside and topside of roof cladding. Inward forces can collapse the roof cladding inwards. Outwards forces are due to positive wind pressure inside the building and negative wind pressure from outside the building. It can lift the cladding from its framing and the entire roof structure from the rest of the building. Hence, it is critical that roof framing, battens, claddings, and flashings are fixed to withstand these pressures.
A difference in air pressure between the inside and outside of walls or the roof can also be caused by wind gusts. This can cause a cyclic or “pumping” action and water can be sucked into a cavity or joint the flashing is covering. A sealant, a clearance gap of up to 5 millimetres, or an anti-capillary offset fold should therefore be included on all flashing edges where they are in close contact with the wall cladding or roof. Flashing should also include expansion joints on long runs to minimise damage during the contraction and expansion of the walls or roof.
Flashing fasteners
Flashing fasteners prevent flutter and noise and avoid the metal cladding flexing or cracking under fluctuating loads.
All roof cladding edges located other than at gutters must have flashings fasteners on both faces, and the number and spacing of these are determined by the “wind load” of a building.
References
- 2020, Flashing guide for architects and detailing professionals, Lysaght
- 2020, Flashing, Build
- 2020, Flashing (Weatherproofing), Wikipedia
- 2016, Flashings: What they are what you should know about them, Houspect
- 2020, Installing flashing, Metalroofingonline.com.au
- 2020, Flashing – ridges, Metalroofingonline.com.au
- 2016, What is metal roof flashing and why do you need it?, Whirlwind Steel